The Silk Road to Mysore
We went on a weekend get away to Mysore, completing our trifecta of the big cities in the state of Karnataka. The other cities are Bangalore, where we live, and Managlore on the west coast. Yet, unlike Karnataka’s other large cities, Mysore has retained its historic charm and elements of its glory-day silk industry. India’s output of mulberry silk is about 14,000 metric tons and the Mysore district accounts for
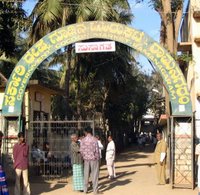
more than half of that production.
The first stop was at the Government Cocoon Market in Armanagaram. The market was a bustling place where various types

of silk cocoons were gathered for inspection and sale. There was no organized tour at the market, but we were very fortunate to catch the attention of an old, leathery silk worker who was more than pleased to share his knowledge. In the market, a zillion or so soft yellow cocoons and hard white cocoons were housed separately in large bins. In a caged area near the entrance, a large scale for weighing sacks of cocoons could be seen. Occasionally, voices would rise up in loud

argumentative clatter. No doubt negotiations were underway over the price of this sack or that sack of cocoons.
Our attention was mainly held by our gracious guide. He shared that a single cocoon could yield 600 meters of silk thread. He cut cocoons

open to reveal the live silk worms inside. Some cocoons were doubles with two silk worms inside. We later learned that in order to “unspin” the single thread of silk made into a cocoon by a worm, the cocoons are dropped into boiling water. Of course that kills the worms, but then the thread can easily be unwrapped and wrapped onto spindles or bobbins.
Our trip to the Cocoon Market only whet our
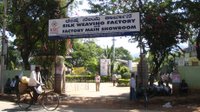
curiosity. What was the process for turning these fuzzy cocoon homes into elegant silk saris? We learned a bit more about the process with a visit to the Karnataka Silk Industry Corporation (KSIC) Silk Weaving Factory.
The cocoons from the Cocoon Market had already been pre-processed into large wheels of raw silk thread. What was involved in that early stage of the silk process remained a mystery. Our knowledge advanced only slightly by what we could glean from our unguided tour of the weaving factory. After signing in and obtaining a chit from the office, a security guard simply opened the gate to the factory and we wandered about unescorted.
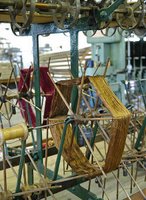
Once inside, we saw that the raw silk thread was wound two or three times into a fine thread by machines that could have been easily described in a Charles Dickens’s novel. Equally so were the silk looms that filled cavernous rooms and rattled with a pounding din that could shake teeth from the best set of dentures. OSHA standards for safety or noise control were nowhere to be found. We were surprised that we could wander about the factory while the machines were spinning, weaving and churning without the slightest
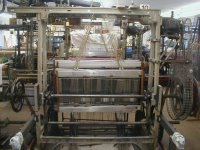
concern for our safety or that of the equipment.
The whole operation was reminiscent of the Southern cotton mills circa 1920. Cheap labor, working under harsh, unsafe conditions for someone else’s profit. Not the stuff of a nation seeking the leadership in a 21st century global marketplace.
0 Comments:
Post a Comment
<< Home